Recycled risk?
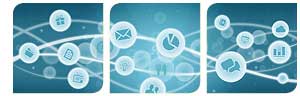
Hitherto untested compounds may migrate from recycled packaging materials into foodstuffs
A variety of substances (including harmful compounds) leach from packaging materials into food – this is why the authorities strictly control and independent laboratories regularly test whether the various components exceed the prescribed limits. With the introduction of recycled packaging materials to the market however, a host of new compounds need to be focused on. An expert from the independent laboratory of Eurofins Food and Feed Testing helped in a study posted on Laboratorium.hu to find out what manufacturers, distributors and consumers should pay attention to.
The average person consumes up to 300-400g of compounds (monomers, oligomers, stabilisers, antioxidants, plasticisers, foaming agents, heavy metals, dyes, manufacturing aids), released from packaging materials, throughout his or her life. Much of these leach into foodstuffs, and they can interfere with human metabolism and damage endocrine organs (they can cause kidney and liver failure and may be carcinogenic in the case of prolonged exposure).
Such components and many other ingredients are regularly tested by suitable accredited laboratories in accordance with European and national regulations, and are regularly checked by the authorities.
To address the growing use of single-use plastic products (among them, of course, packaging materials) and to stop and manage the waste output which is a serious threat to the environment, the European Green Deal prescribes that the proportion of packaging materials that is recycled (by way of material and energy recovery, as well as composting) should rise to 65 percent by 2025, and accordingly, a certain percentage of recycled raw materials will have to be used on a mandatory basis in the future.
However, the process, which deserves to be fully supported, poses new challenges, as recycled packaging materials may release unknown and so far untested compounds into foodstuffs.
We interviewed about the above Dr. Ágnes Kovács, an expert at Eurofins Food and Feed Testing Budapest Kft., a leader in the testing of packaging materials: she summed up the most important facts on the basis of thousands of analyses and years of laboratory research experience.
What does the EU law say?
The European Union recognised the problem, therefore it has already formulated the basic requirement for all recycled plastics coming into contact with food – regardless of product group – in Commission Regulation 2022/1616 on recycled plastic materials and articles intended to come into contact with foods, said Ágnes Kovács.
Accordingly, plastic packaging materials may only be produced using via processes whose safety has been verified by the European Food Safety Authority (EFSA). In the case of new technologies, it must be demonstrated (e.g. by the Challenge test) that the process effectively removes chemical contaminants. Thereafter European Commission authorises, and publishes a list of, the recycling technologies whose assessments have produced favourable results. Only PET recycling technologies have been authorised to date, and there is no suitable process for polyolefins (PE, PP) yet.
Why can recycled packaging pose a greater hazards?
The reason why recycled plastics pose a higher food safety risk than "virgin" plastics is that on the one hand, their traceability in the supply chain is compromised (we do not know the raw materials, their purity, origin, etc.), and, on the other hand, the objective of ensuring that plastic waste collected for processing is made up exclusively of plastics manufactured in accordance with Regulation (EU) No 10/2011 or recycled in accordance with Regulation (EU) No 2022/1616, cannot be fully achieved.
Other packaging materials (e.g. packaging waste from cleaning products or cosmetics) may be mixed in with the recycled plastics – Ágnes Kovács says – and there may also be a problem if a bottle originally intended for food packaging was used for storing other, possibly even hazardous, substances or residues.
Plastic packaging materials contain traces of substances that have come into contact with them, which in many cases are absorbed into the plastic and cannot be removed by washing (besides the materials stored in the packaging, particular attention must also be paid to the inks used for printing!).
Another potential problem is that plastics are exposed to high temperatures during recycling and remoulding, which may cause contaminants to degrade and/or oxidise, and even new substances to be formed. Additives used in plastics (designed for only one thermal cycle) can also degrade.
Accordingly, the quality of plastics that are recycled more than once deteriorates: they contain more oligomers, degradation products and pollutants, but exactly what, is usually unpredictable.
Which plastics pose greater risk for recycling?
Recyclability depends to a great extent on the type of polymer concerned: PET is a more suitable raw material, less likely to absorb contaminants, and high temperatures can be used during production which enables the removal of contaminants, while polyolefins bind contaminants better, are produced at lower temperatures and are therefore more difficult to remove – Eurofins's specialist explained.
Recycled plastics can also be used in producing multi-layer packaging, where the lower quality recycled layer is not in direct contact with the food, as it is separated from it by a functional barrier layer. The barrier layer (e.g. aluminium) prevents the ingredients from migrating into the food, because they cannot permeate through this layer. This technique also makes recycled polyolefins suitable for the production of food packaging.
What are the things that a manufacturer should check? Which compounds can be dangerous and why?
The conformity of the material must be verified by the manufacturer or distributor by what is known as migration testing, carried out regularly by an accredited laboratory, Ágnes Kovács said. The same testing requirements apply to these materials as to products made from non-recycled raw materials; they are analysed for the same parameters, including total migration, specific individual components, typical monomers used in the manufacture of the material, and targeted additive migration analyses. (In PET, for example, these include monoethylene glycol, diethylene glycol, terephthalic acid, isophthalic acid, metals).
In addition, it is particularly important to examine the migration of non-intentionally added substances (NIAS), as in their case there is greater uncertainty about the raw materials and potential contaminants. This group includes contaminants of raw materials, oligomers, degradation products, reaction products.
These may be present in recycled plastics in larger numbers and quantities, and contaminants from previous use may also be found. These components are not known in advance and the laboratory's first task is to identify them qualitatively. In order to produce safe packaging, it is essential to know what substances are present (or as many of them as possible) and to be reassured that they do not pose a health hazard. Toxicological evaluation is therefore an important part of the test, since there are no migration limits for the majority of the components so detected.
These components are tested by few laboratories, Eurofins however, thanks to its many years of experience, can perform these measurements highly reliably.
How does the laboratory carry out its investigations – what does it look for in packaging materials?
The laboratory tests are carried out with the help of so-called food simulants, materials with properties similar to the food products that come into contact with the packaging materials and have similar impacts on them.
The migration tests and analyses are always based on, and model, the most unfavourable conditions of use. On the one hand, the total quantity of the components ending up in the solution is measured. This total migration test provides information not on the quality of the ingredients prone to migrate, but on the inertness of the packaging material to the food.
Various ingredients or contaminants, mostly monomers, plasticisers, antioxidants, heavy metals are analysed in specific migration tests. This requires a variety of analytical techniques, including liquid chromatography, gas chromatography, spectrophotometry and various metal analysis methods; depending on the target component. The identification and quantification of unknown components migrating from the packaging materials into the model solutions an important part of the tests. They are separated from the other components by various chromatographic methods and identified by their mass spectra.
What impacts may the new deposit return system introduced in Hungary this year be expected to have on the uptake of recycled food packaging?
Targets for the collection of single-use plastic products for recycling are laid down in Directive 2019/904 ("SUP Directive"): of up to three litre single-use plastic beverage bottles (including caps and lids) must be collected in quantities equivalent to 77% by weight of the volume placed on the market in a given year by 2025 and 90% by weight of the volume placed on the market in a given year by 2029.
A large proportion of these will most likely be recycled into food packaging. Food manufacturers may also be motivated by consumer expectations or social responsibility, also encouraging them to use recycled packaging materials. Their proportion is thus likely to grow with in the wake of the introduction of the deposit return scheme, which also justifies regular testing, the laboratory expert said.
Packaging is not an enemy!
It is important to stress however, that modern food industry would be unthinkable without packaging materials: they keep food together and protect it from environmental impacts (and vice versa), prolong their shelf-life, minimise the risk of their infection and contamination and inhibit the growth of micro-organisms in the product. Moreover, packaging materials must withstand cold and heat, have adequate permeability for the foodstuffs packaged in them, be resistance to preservation processes and handling and carry the mandatory labelling information required by law (net weight, minimum shelf life, prescribed storage conditions, nutritional details, etc.), let alone marketing messages they have to carry. The environmental aspect is another increasingly important requirement – this is why, for example, an increasing proportion of non-recyclable packaging materials have to be biodegradable.
Packaging is therefore not an enemy – Ágnes Kovács emphasised – adding that in case the rules on production and distribution are followed, and if regular official and laboratory tests and analyses are carried out, they do not pose a threat to people. Rather they serve to improve the quality of life.
The testing methods developed and carried out in laboratories make it possible to effectively identify, and avoid the use, of substances that are unsuitable for food packaging, sometimes toxic. This will help increase the safety of packaged food products.